Safety at work is directly related to return on investment, according to the American Society of Safety Professionals.
So how do you create a safe working environment, and increase ROI in the process?
The answer is simple: Plan regular safety inspections and safety audits. At first glance, these two terms may sound synonymous.
However, they differ in scope and the parties responsible for their execution.
In this article, we’ll compare a safety inspection vs. safety audit and provide a glimpse into how each checklist typically looks.
Plus, we’ll explain how to streamline each process by ditching paperwork checklists and going digital.
Table of Contents
Does your business use safety forms?
Try doForms for free!
What Is A Safety Inspection?
A safety inspection is a detailed, documented procedure used to identify potential risks in the working environment. The ultimate goal of a safety inspection is to eliminate hazards and unsafe conditions and prevent workplace accidents or injuries.
A safety inspection also examines employee behavior at work to identify unsafe practices. Examples include:
- Use of inappropriate or defective equipment
- Failure to maintain a clean and clutter-free working environment
- Use of ladders instead of scaffolds
- Failure to wear protective equipment
- Failure to secure electrical wires or other hazards
Safety inspections focus on equipment, locations, and people.
They are typically performed by:
- Internal safety experts
- Internal or independent environmental health and safety (EHS) professionals who are responsible for planning, implementing and enforcing environmental, health, and safety policies and procedures
- Third-party organizations such as Occupational Safety and Health Administration (OSHA)
How often should you conduct safety inspections?
According to OSHA’s safety inspection guidelines, the recommended frequency of safety inspections varies based on the industry.
OSHA recommends that companies in the construction businesses, for example, conduct safety inspections on a weekly basis. General guidelines for other industries are monthly for specific areas and quarterly for full site inspections.
What Is A Safety Audit?
A safety audit evaluates the efficiency of a company’s safety systems, training programs and reporting processes to ensure they meet safety goals and requirements.
A safety audit focuses on the following:
- Meeting industry best practices and regulatory requirements
- Documented evidence of compliance
- Correlation between company training and behavior
Safety audits focus on processes, operations, and programs.
If your company does not have a dedicated EHS expert in-house to conduct safety audits, you can hire a third-party consultant to conduct the audit for you. Safety professionals possess knowledge of both applicable safety regulations and company programs, which enables them to make an accurate assessment.
Based on the findings from a safety audit, the auditing person or team suggests recommendations to remedy issues, so respective supervisors and managers can take corrective actions.
Safety audits are typically performed more seldom than safety inspections, usually once or twice per year. However, depending on the industry, work environment, and other factors, some companies may conduct an audit more frequently.
OSHA does not regularly access audit reports but may request access in some circumstances. For example, if a fatal accident occurs at the workplace, OSHA may request company safety audits to refer to in an investigation.
Keeping all of your safety audit checklists and corrective action reports accessible in one place will help ensure you’re able to:
- Follow up on the outcome of every audit and the respective measures taken
- Provide immediate access to your safety documentation upon request from third-party organizations conducting safety investigations on your site
Keeping this type of paperwork organized, stored, and accessible month after month, year after year, is no small feat.
The best way to keep inspections, audits, reports, and other data organized and available when you need it? Mobile forms — which we’ll get to soon!
Ready to say goodbye to paper forms?
Try doForms for free!
Safety Inspection vs. Safety Audit: Key Differences
So, what exactly is the difference between a safety inspection and a safety audit, and what similarities do they share? Let’s take a look:
Similarities
Goals: Both safety inspections and safety audits are performed to ensure a safe working environment.
Use of checklists: Both use detailed checklists based on industry best practices and OSHA requirements.
OSHA requirements: OSHA accepts safety inspections and safety audits as mandatory elements of an effective safety plan.
Differences
Scope: A safety inspection focuses on equipment, locations and employee behavior at work. A safety audit reviews and analyzes safety strategies and programs.
Parties in charge: A safety inspection is performed by a person who is familiar with the company’s working environment or by a regulatory agency. A safety audit is conducted by independent parties (outside the respective department or outside the company).
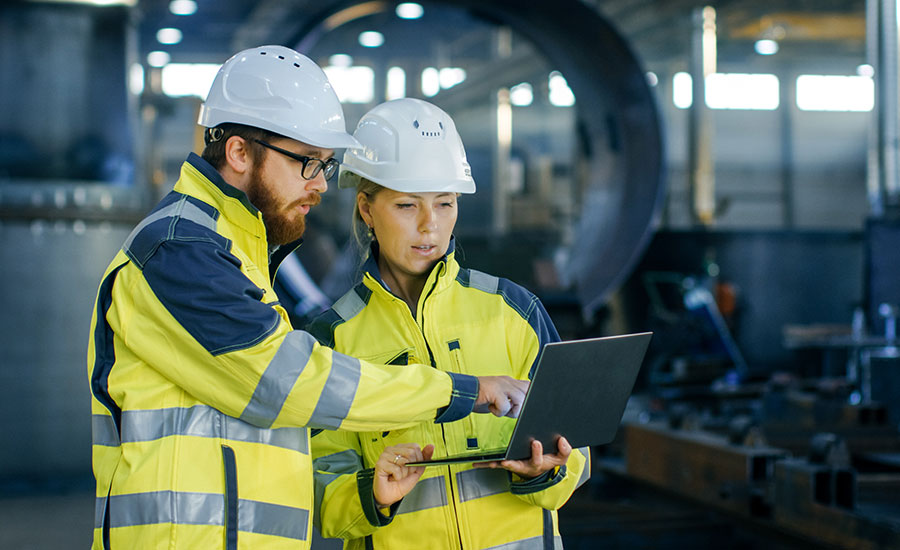
Safety inspections and safety audits aim to provide safety at the workplace but differ in scope, frequency, and the experts in charge of each one
What Does A Safety Inspection Look Like?
Items on a safety inspection checklist can vary depending on the industry, environment, project and other factors, but common focus areas include:
- Production equipment such as cutters, presses, robotics
- Pressurized equipment such as boilers, valves, hydraulics
- Powered equipment such as electrical motors, compressors, engines
- Personnel support equipment such as platforms, scaffolds, ladders
- Fire protection equipment such as sprinkler systems, extinguishers, hoses
- Personal protective equipment such as safety glasses, gloves, hard hats
- Hazardous products such as explosives, corrosives, flammable products
- Psychological hazards such as fatigue, poor communication, conflicts
- Hygiene and first aid such as first aid supplies, safety showers, drinking fountains
- Walkways and roadways such as ramps, aisles
A detailed inspection checklist used regularly helps prevent accidents down the line, whether due to employee error, equipment malfunction, or other common risks.
Also Read:
What Does A Safety Audit Look Like?
A safety audit checklist typically focuses on questions such as:
- Can employees access equipment and machinery manuals?
- Does the equipment meet safety standards?
- Are employees familiar with the fire escape plan?
- Is ventilation adequate in the workplace?
- Are vehicles and machinery regularly maintained?
- Are employees trained on machines and equipment?
- Are hazardous materials disposed of properly?
- Are chemicals divided and stored by compatibility?
- Are electronic devices managed properly?
- Are workers trained to recognize hazards and how to control them?
- Do employees know the procedures to report injuries and incidents?
A comprehensive audit checklist will help you locate vulnerable programs and operations and act to improve safety within your company.
Creating Digital Safety Checklists With doForms
It’s no secret that both safety inspections and safety audits are extremely important to workplaces across industries — to help keep employees safe, ensure equipment is used correctly and prevent workplace accidents before they happen.
The downside of filing these checklists on a regular basis? Time-consuming paperwork that can easily get misplaced, disorganized and even damaged.
doForms is a mobile forms software solution for business forms and data collection. Why spend time and resources on paperwork when you can go digital?
Choose from our library of templates and start editing, or create your own custom forms, for safety inspections, safety audits, maintenance reports, work orders, and more!
Whether you’re sitting in an office, walking through a construction site or in the middle of your daily commute, you can create, edit, send and store our mobile forms anywhere, from any device.
doForms offers efficient, reliable data collection and transfer. Send safety reports to third-party contractors, view a history of maintenance work on your equipment, track off-site locations, and more. All data is available in real-time and safely stored for later use.
From affordable pricing plans and out-of-the-box integrations, our scalable mobile forms solution offers increased productivity, better organization and cost savings.
doForms extensive features include:
- iOs and Android compatibility
- Standard and custom templates
- Unlimited mobile forms
- Unlimited data storage
- Real-time job dispatch
- Device-based GPS tracking
- Calendar-based job scheduling
- Secure workflow and reporting
- Barcode label printing
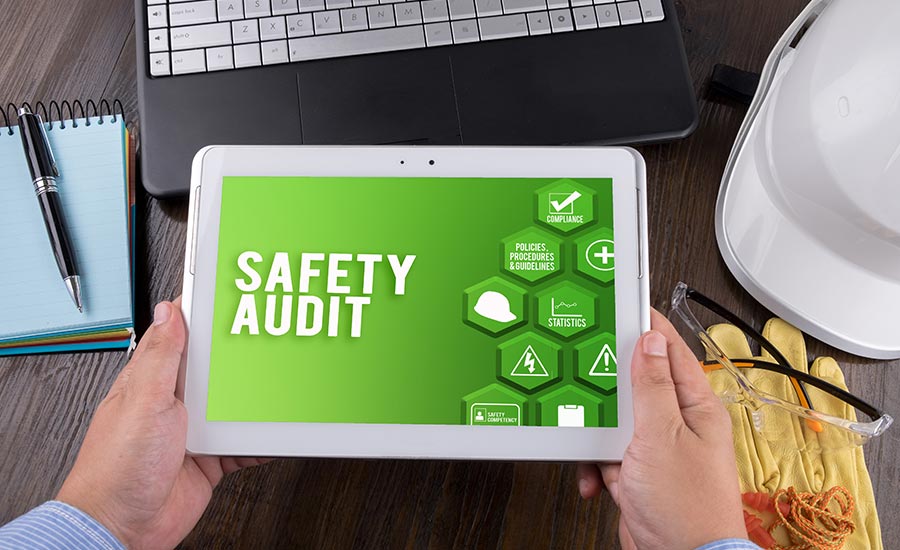
Safety inspections and safety audits have never been so easy. Use a template from doForms’ library or create your own form and fill out safety checklists on the go.
Safety Inspection vs. Safety Audit: Key Takeaways
While both safety inspections and safety audits aim to improve safety in the workplace, inspections typically focus on people and equipment, while audits examine processes, programs, and training systems.
Inspections and audits are both vital to ensuring safety in the workplace and preventing potential accidents before they happen. Not to mention, work safety is directly related to business ROI.
Replace time-consuming and unorganized paper checklists with digital checklists for easy access, storage and retrieval to safety inspections, safety audits, and other reports.
With doForms, you can:
- Create custom safety inspection and safety audit checklists
- Store your data in a secure location for easy access by approved parties
- Access data in real-time from any location or device
- Share reports quickly and easily with employees, third parties and more
- Reduce paper costs and improve workflow
- Decrease time-consuming tasks and improve productivity
At doForms, we offer a 30-day free trial. Start creating and sharing your custom forms today.