From filling out order labels to counting and confirming new stock, a warehouse receiving process checklist is key to efficient inventory management.
In this article, we’ll explain the warehouse receiving process, share benefits and provide a full checklist.
Plus, we’ll explain how to simplify your daily checklists so warehouse operators can fill out, save and upload forms wherever they’re at in the warehouse.
Your warehouse receiving process checklist should include:
- Documentation
- Receiving And Inspection
- Unloading
- Storing Inventory
Table of Contents
Digitize your warehouse receiving checklists.
Try doForms for free!
What Is A Warehouse Receiving Process Checklist?
A warehouse receiving process checklist is a list of tasks that must be completed before storing inventory in your warehouse.
Typically used by warehouse managers and receiving staff, this checklist provides guidance regarding what needs to be inspected in new shipments, so that inventory can be accurately monitored and managed.
The checklist outlines key steps, such as tracking shipments, receiving and unloading stock, inspecting inventory for damage, testing for quality control and keeping inventory in its designated area.
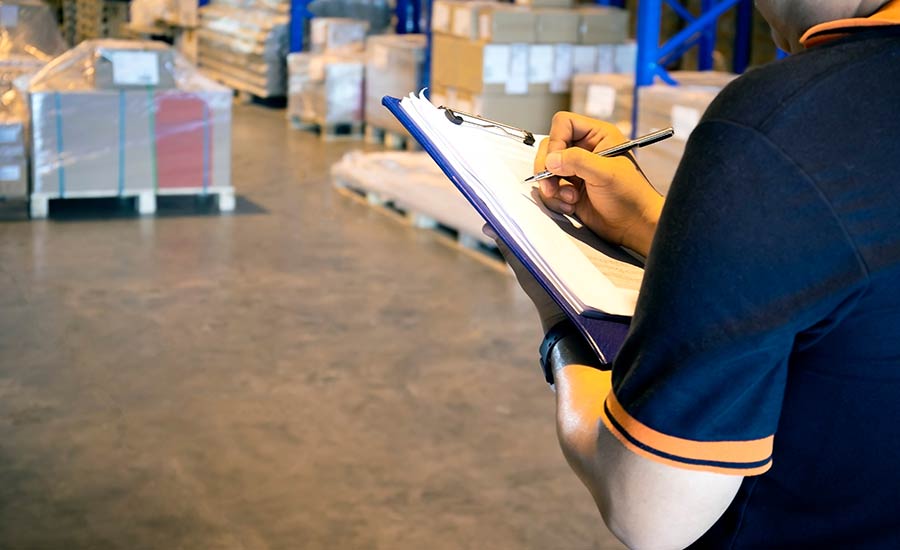
Warehouse managers and receiving staff utilize warehouse receiving process checklists when shipments arrive in the facility
What Does The Warehouse Receiving Process Look Like?
The warehouse receiving process typically includes four main steps:
1. Complete Pre-Receiving Tasks
Pre-receiving tasks ensure that your warehouse is prepped and ready for incoming shipments.
Pre-receiving tasks include:
- Identify the number of inventory items in each shipment
- Determine storage requirements based on product dimensions, cargo labels and how many packages are loaded onto each pallet
Typically, operators fill out a warehouse receiving order (WRO) label and attach it to each shipment, making sure the barcode is visible.
A warehouse receiving order label allows your warehouse operators to scan the shipment’s barcode using a warehouse management system (WMS).
This step is paramount in ensuring that your shipment is accurate and stored in the proper area in the warehouse.
If you’re working with a third-party company (3PL), be sure to check their pre-receiving requirements and inventory delivery process.
2. Receive And Unload Shipments
To streamline the receiving and unloading process, have your warehouse receiving operators meet the shipper at the loading dock to discuss any concerns (like product damages) or questions regarding shipment.
To unload shipments, you’ll want the help of warehouse material handling equipment such as pallet jacks and forklifts, to carry large cargo.
(Speaking of forklifts, check out our forklift safety checklist!)
3. Count Inventory
As the cargo is unloaded, your warehouse receiving staff should evaluate and verify the contents of each delivery. This includes the integrity of seals, product codes and SKUs, quantity and overall condition of the cargo.
To streamline this process:
- Count pallets or boxes instead of checking individual items
- Perform random inspections
- Utilize an inventory scanner system to easily scan goods with a smart device
4. Store Inventory
This step varies for each warehouse and largely depends on:
- Your warehouse type (manual or automated)
- Your warehouse space
- The type of inventory you have (for example, if you’re storing small parts, invest in standard shelving systems and industrial cabinets)
- Whether you rely on a 3PL partner to store your inventory
Complete Warehouse Receiving Process Checklist
Here’s what your warehouse receiving process checklist should include:
1. Documentation
- Make sure warehouse operation procedures are documented and updated whenever a new task arises
- Prepare the receiving documents before the shipment arrives
- Check the shipment’s quantity, condition and description before marking it as complete on the receiving report
- Inform your warehouse manager if there are any irregular report backlogs
2. Receiving/Inspection
- Check key shipment details such as the material, description, purchase order number and quantity of the items received
- Make sure the shipment’s dimensions are accurate. Cross check the dimensions against the indicated specifications.
- Check if the shipment has fragile or biohazard markings
- Check the shipment for potential shipping damages, including physical, contamination or infestation damages. If the product is in good condition, forward it to the unloading section.
3. Unloading
- Make sure that warehouse vehicles are stabilized and turned off before you load and unload inventory
- Utilize appropriate lighting in loading areas
- Ensure loading areas are hazard-free and place necessary loading and unloading zone signs to prevent accidents
- Make sure the loading area pathways are free of traffic. For example, forklift traffic must be designated as one-way paths.
4. Inventory
- Make sure the number of products in each shipment is correct
- Perform spot checks to determine whether inventory is properly slotted in its designated area
- Make sure that your stock records reflect inventory shelf-life information
- Perform weekly spot checks to verify product condition and quantity
Create your warehouse receiving process checklist today with doForms!
Try doForms for free!
Benefits Of A Warehouse Receiving Process Checklist
From preventing dead stock to ensuring you have enough storage space for inventory, a warehouse receiving process checklist helps you:
1. Prevent Stockouts And Overstocking
Stockouts occur when you don’t have enough inventory to fulfill orders.
Stockouts can lead to negative reviews that can hurt your brand’s reputation and can cause customers to look elsewhere to purchase the out-of-stock product.
In fact, 21% of consumers will turn to other brands to purchase an out-of-stock item instead.
On the other hand, overstocking or dead stock can leave your business with an inventory surplus that won’t deliver a return on investment, let alone a profit.
A streamlined warehouse receiving process checklist helps prevent inventory issues from occurring.
2. Prevent Product Damage
Product damage can result from contamination, infestation or physical damages.
Following a warehouse receiving process checklist allows you to inspect and QA inventory before it’s shipped to your customers.
3. Improve Inventory Storage
Whether it’s storing nuts and bolts in industrial cabinets or storing heavier cargo in pallet racks, a warehouse receiving process checklist ensures your inventory is kept safely in its proper storage area.
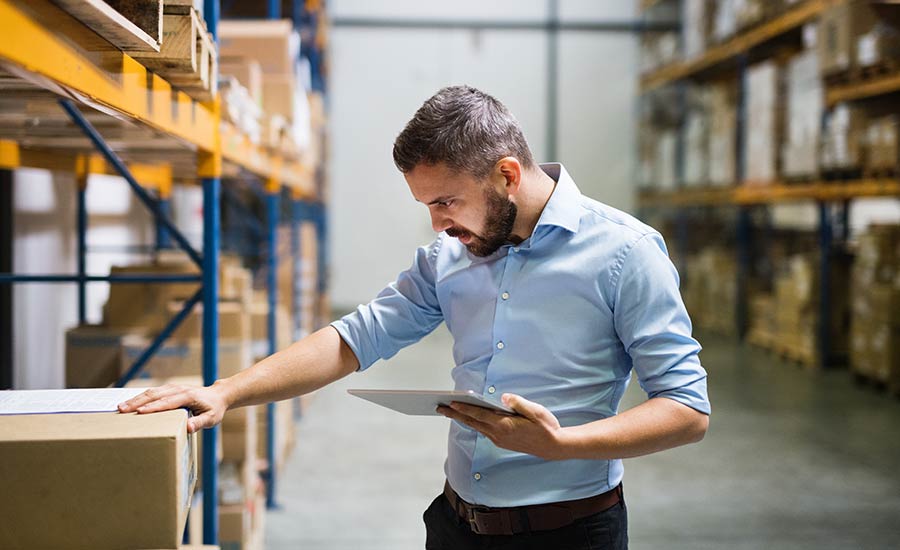
A warehouse receiving process checklist ensures you don’t receive damaged inventory
Warehouse Receiving Best Practices
From decluttering your warehouse space to investing in warehouse automation, here are five tips to improve your warehouse receiving process.
- Build a receiving schedule: Identify the volume and materials that are coming in your warehouse so you can prepare proper storage areas.
- Optimize your warehouse space: Organize and optimize your existing warehouse space by eliminating clutter and utilizing dead corners and empty slots to improve operational workflows and minimize inventory and labor costs.
- Upgrade warehouse receiving equipment: Boost dock-to-stock cycle time and reduce inaccurate inventory when you eliminate labor-intensive manual tasks with automation (think warehouse management systems that can easily scan your inventory).
- Isolate damaged goods: Seclude damaged inventory by placing it in your warehouse quarantine area, to prevent operators from sending out damaged products to customers.
Streamline Your Checklists With doForms
From documentation and inspection to unloading and checking inventory, the warehouse receiving process has many different steps to ensure successful order fulfillment.
doForms is a mobile forms solution that upgrades your paper warehouse receiving checklist into a streamlined and digitized system, helping you save as much as $8,000 per year on printing alone!
In addition to reducing costs, digital checklists allow your warehouse employees to fill in reports on the go, wherever they’re at in the warehouse.
You can create, modify, save and send your warehouse receiving checklists on the cloud, all from a simple touch of your tablet and smartphone.
Oh, and did we mention that you can import data into your forms, export collected data, and access your checklists even when you’re offline?
In addition to warehouse receiving checklists, which you can easily modify when a new task arises, doForms allows you to:
- Report near misses in the warehouse
- Create a gemba walk checklist to evaluate the workplace and identify problem areas
- Communicate warehouse equipment repairs and inventory issues in real-time
- Create preventive maintenance reports and warehouse maintenance checklists
- Manage warehouse inventory, operational costs, sales and employee performance reports
- Export warehouse employee payroll forms and modify templates
- Access employee time sheets and schedules at any time, from any smart device
- Minimize the risk of sharing sensitive information such as employee payroll and appraisals, with features such as encrypted security through HIPAA compliancy and multi-factor authentication
Ready to go the paperless route?
Try doForms for free!
Wrapping Up On Warehouse Receiving
A warehouse receiving checklist includes a list of tasks that your warehouse employees must complete before storing inventory from each new shipment.
By ensuring that all incoming shipments are documented, checked and properly stored, you can minimize potential product damages, reduce the risk of overstocking and stockouts and ensure that your warehouse operations run smoothly from receiving to dispatch.
While traditional warehouse checklists are bulky, disorganized and costly, switching to doForms allows you to improve organization, reduce paper costs and streamline operations within your warehouse.
Choose from our library of templates or create your own custom forms from scratch. Access your secure online portal anytime, from any location, and use the reporting and analytics tool to gain real-time visibility into your warehouse data.